1. What is Polycrystalline Diamond (PCD) Tooling?
Polycrystalline Diamond (PCD) is a synthetic material made by sintering diamond particles with a metallic binder under extreme temperatures and pressures. The result is a cutting material that is incredibly hard, wear-resistant, and highly durable. PCD tooling is widely used in industries that require high-performance cutting tools capable of withstanding abrasive and demanding conditions.
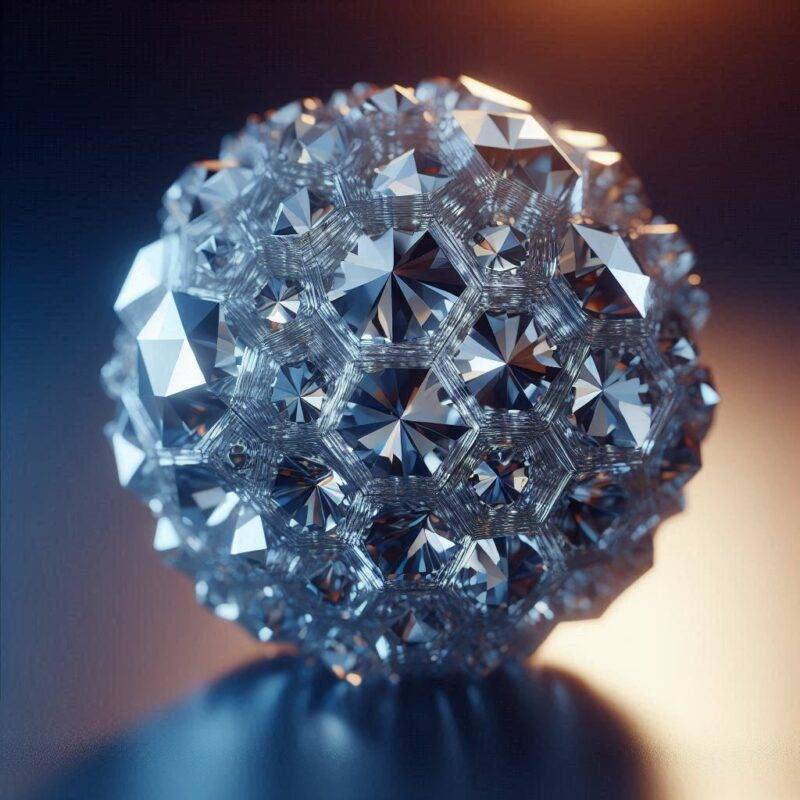
2. The Advantages of PCD Tooling
PCD tooling offers several key advantages over traditional cutting materials like carbide or steel. The most notable benefits include:
- Exceptional Hardness: PCD is one of the hardest materials on earth, making it ideal for cutting hard and abrasive materials like MDF, HDF, chipboard, and composite materials.
- Superior Abrasion Resistance: PCD tools wear down at a much slower rate than conventional carbide tools, offering a longer service life and reduced downtime.
- Heat Resistance: PCD maintains its cutting edge even under high temperatures, preventing material buildup and improving overall tool performance.
- Cost Efficiency: While the initial investment in PCD tools may be higher, the extended lifespan and reduced frequency of tool changes can lead to significant cost savings over time.
3. PCD Tooling Applications
PCD tooling is used in a variety of machining operations, especially those involving abrasive materials. Common applications include:
- Sawing: PCD saw blades are ideal for cutting composite materials such as MDF, HDF, and laminated surfaces. They are commonly used in panel saws and sliding table saws to improve cutting efficiency and tool longevity.
- Routing and Drilling: PCD tools are also effective in routing and drilling operations, where precise, high-speed cuts are required. Whether working with composite materials, plastics, or wood, PCD’s durability ensures a long tool life and minimal maintenance.
- Profiling: In woodworking and composite industries, PCD profiling tools shape edges and surfaces without losing sharpness, maintaining consistent quality over long production runs.
4. PCD vs. Tungsten Carbide Tools
PCD and tungsten carbide are both popular materials for cutting tools, but PCD has distinct advantages in certain applications:
- Longevity: PCD tools have a much longer lifespan than carbide tools. For instance, PCD saw blades can last up to 10 times longer than traditional carbide blades, resulting in fewer tool changes and less downtime.
- Hardness: While tungsten carbide is hard, PCD is harder, making it better suited for cutting highly abrasive materials.
- Heat Management: Polished PCD tips are effective at preventing heat buildup during cutting, which improves tool performance and prevents material buildup.
5. Choosing the Right PCD Tool for Your Application
When considering PCD tooling for your machining processes, it’s important to choose the right type of tool for the job. Here are some common types of PCD tools:
- PCD Diamond Saw Blades: Perfect for cutting through abrasive materials like MDF, HDF, and particleboard. These blades provide exceptional cutting precision and durability, making them ideal for high-volume production environments.
- PCD Premill Cutters: Used primarily in edge banding machines for pre-milling surfaces like MDF or particleboard before the application of edge banding. These cutters can run for up to a year without requiring sharpening, saving both time and money on tool maintenance.
- PCD Drills and Routers: For precision drilling and routing in composite materials, PCD tools provide consistent results and long-lasting performance.
6. Why Switch to PCD Tooling?
Switching to PCD tooling can offer several benefits for manufacturers, including:
- Lower Operating Costs: With extended tool life and fewer tool changes, PCD tooling helps reduce overall operating costs. In high-volume environments, these savings can add up quickly.
- Improved Productivity: With fewer interruptions due to tool wear, production lines can operate more efficiently, increasing overall output.
- Reduced Maintenance Costs: The durability of PCD tools means less frequent maintenance, which can lower the total cost of ownership for cutting tools.
.
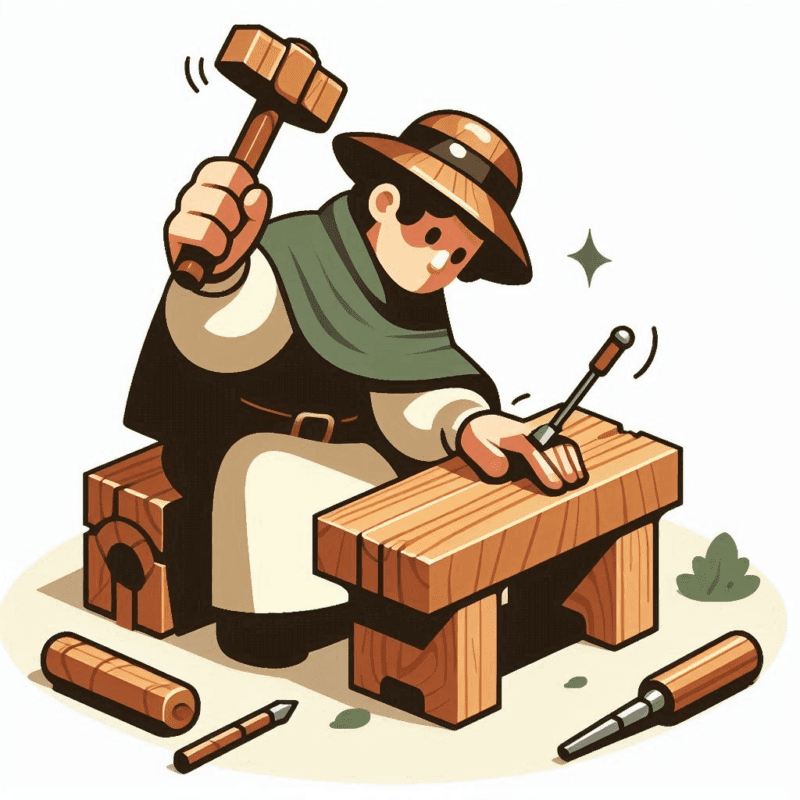
8. Conclusion
PCD tooling is a powerful solution for industries that require precision, durability, and cost-efficiency in their machining operations. By offering longer tool life, superior abrasion resistance, and exceptional hardness, PCD tools are ideal for cutting abrasive materials and enhancing production efficiency. Whether you’re involved in woodworking, composite materials, or other high-precision industries, switching to PCD tooling can provide significant long-term benefits.
To learn more about PCD tooling or to get expert advice on selecting the right tools for your needs, contact us today. Our specialists are ready to guide you through the process and ensure you get the most out of your machining operations.