Tool Nose Radius (R-angle) refers to the rounded corner radius at the cutting edge of a tool.
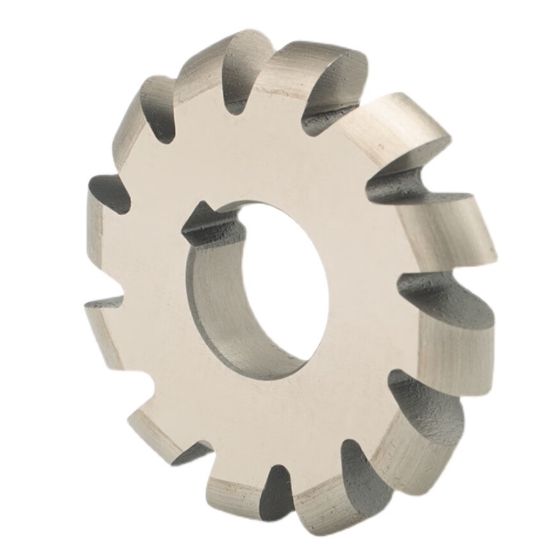
In tool design and application, the tool nose radius is a critical parameter. It defines the curvature at the tool’s tip, directly influencing cutting performance and tool life. In practice, the size of the R-angle must be selected based on specific machining requirements and workpiece materials to achieve optimal results.
Impact on Cutting Forces
The design of the R-angle significantly affects cutting forces. A larger R-angle reduces the contact area between the tool and workpiece, thereby lowering cutting forces and ensuring a more stable machining process. This is particularly important when machining high-hardness materials or performing precision operations, as excessive cutting forces can accelerate tool wear, cause damage, and compromise machining accuracy and surface finish.
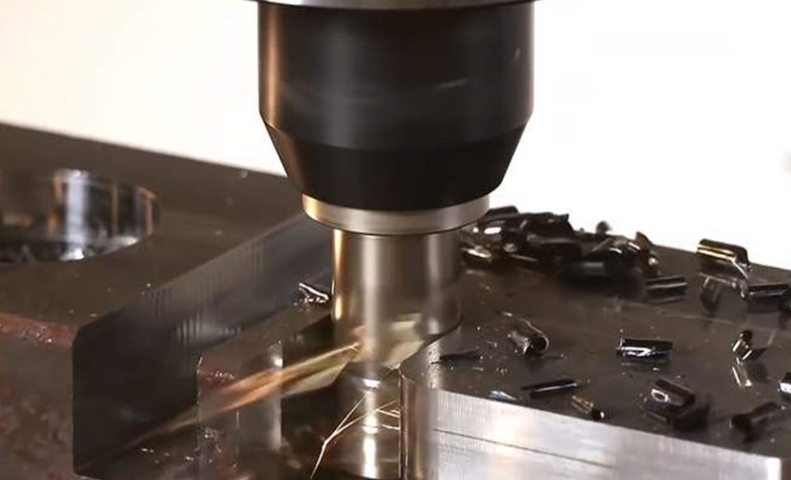
Tool Durability
The R-angle also plays a key role in tool longevity. The rounded edge helps distribute cutting stresses, reducing wear. Especially during interrupted cuts or when machining uneven surfaces, an appropriately sized R-angle effectively prevents edge chipping and breakage, extending tool life.
Surface Quality
Additionally, the R-angle is closely related to machined surface quality. A smaller R-angle allows for more precise control over chip thickness, resulting in higher machining accuracy and superior surface finish. This is crucial for high-precision applications, such as aerospace and automotive manufacturing.
Conclusion
In summary, the tool nose radius is a fundamental parameter in tool design, directly affecting cutting performance, durability, and surface quality. In practical applications, the R-angle must be carefully selected based on machining conditions and workpiece materials to achieve the best possible results.