Furniture is the most important part of home improvement, and it also costs a lot. Therefore, furniture has become the focus of attention. 3 important factors that determine the quality of panel furniture: wood, surface, edge banding.
The quality of the edge banding determines the service life of the furniture. It not only protects the edges, waterproofs, seals the release of harmful gases and reduces deformation, but also plays a role in beautifying and setting off the furniture.
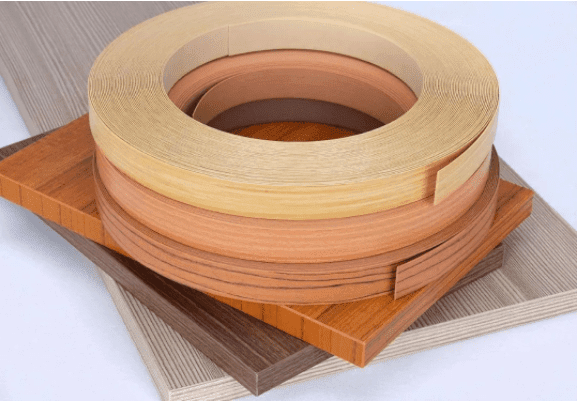
1. How to identify high-quality edge banding?
(1) The edge banding is consistent with the color and pattern height of the plate.
(2) Edge banding thickness
Mainly there are several specifications of 0.3mm, 0.5mm, 1mm, 1.5mm, 2mm. Usually the cabinet body has a thin edge of 0.3mm or 0.5mm, and the bright side and door panel have a thick edge of 1mm or 2mm. There is no rounding on the thin side, the board and the board are assembled more closely, and the thick side is rounded, round and not cut.
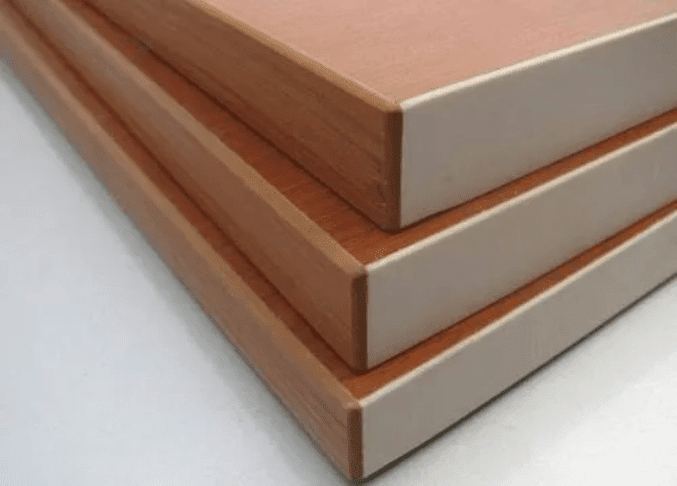
(3) The high-quality banding edge is delicate and smooth. It has a good hand feeling, the banding line is straight, the board and the banding edge are tightly seamed, without protrusions, no chipping, and no obvious glue line
The linear edge banding machine can complete multiple processes such as edge banding, end cutting, trimming, corner rounding, polishing, etc., to ensure the most accurate size. However, some small workshops use manual edge banding and trimming with a utility knife. Due to uneven gluing and uneven sealing, the edge banding is easy to loose and degummed over time.
(5) Use the remaining material board, lift the edge banding with a knife, and then tear it apart forcefully, check whether the bonding strength between the edge banding strip and the hot melt is reasonable and uniform, and whether there is any lack of glue.
(6) Whether the edge banding and trimming are whitish
In particular, whether the edge banding surface at the small arc of the plate is seriously white, and whether the trimming background color of the edge strip is close to the surface color of the plate.
PVC edge banding strips are mainly made of PVC and calcium carbonate plus additives. If the calcium carbonate content is too high, trimming and bending whitening will occur, and this whitening will not be caused by the edge banding. It will recover after straightening, and it will be more obvious to darker ones, and it will be easy to crack under external force.
(7) Whether the side of the sealing edge is even after trimming, without jagged edges
The trimming knife is too blunt; or the edge banding is too hard; or the speed of the hot melt adhesive and the feeding material are not well coordinated when the edge is being sealed, and the edge banding is not completely bonded to the board, causing floating and edge jumping phenomenon.
(8) The edge glossiness of the edge band after trimming and grinding is poor
(9) Whether there is any miscellaneous spots, if there are miscellaneous spots or fine hair pinholes, it may be made of recycled miscellaneous material PVC
(10) Other hidden properties
Anti-aging ability, resistance to yellowing, scratch resistance, resistance to cleaning with fine detergent, not easy to change color under light, weather resistance (not easy to shrink and expand due to environmental and temperature changes).
The two major difficulties in edge banding are the narrow edge and the end. Whether the edge banding is good or not depends mainly on these two places.
2. Type of edge banding?
The edge bands are made of acrylonitrile, butadiene, styrene copolymer (ABS), polypropylene (PP), polyvinyl chloride (PVC), polymethyl methacrylate (PMMA) and wood seals. Wait.
(1) Wooden edge banding
The above good natural birch, oak, maple, beech, cherry and other woods are machine-processed and cut into thin wood edge bands. It is common in woodwork on site, glued with white latex and fixed with nails, and painted after polishing. There is solid wood strips edge banding machine which can banding up to 12mm thickness.
(2) PVC edge banding
The most mainstream edge banding material. It is mainly made of polyvinyl chloride. Its surface has wood grain, marble, cloth grain and other patterns and patterns, and the surface has soft luster, which has the real and three-dimensional sense of wood; it has a certain degree of smoothness and decoration, and has a certain degree of heat resistance, Chemical resistance, corrosion resistance, surface hardness.
Disadvantages: Polyvinyl chloride is a polymer with very poor thermal stability. In order to facilitate molding, many additives such as plasticizers, heat stabilizers and processing aids must be added to the formulation. Most additives contain different levels of harmful substances and will produce hydrogen chloride, aromatic hydrocarbons and other harmful substances during processing.
(3) ABS edge banding
Currently one of the most advanced materials in the world, it is commonly used for edge banding of high-end furniture.
The most common are PVC and ABS edge banding strips, of which ABS edge banding effect is better, but the cost is also higher.
The comparison between PVC and ABS edge banding is as follows:
1. ABS edge banding does not add any fillers (such as calcium carbonate) during the production process, so the rounded corners after trimming are very smooth and beautiful, and the surface has strong impact resistance; PVC is added with high carbonate fillers. White edges are easy to appear when trimming, but they are wear-resistant.
2. The service temperature of ABS products is -40℃-100℃, and the service temperature of PVC products is -30℃-80℃. Because ABS has a lower shrinkage rate and a higher heat distortion temperature, it has better dimensional stability and will not shrink or expand excessively due to large temperature differences.
3. ABS edge banding has a strong resistance to chemical corrosion, and it is always new. Coffee, soy sauce, alcohol, etc. will not cause any damage to its surface; while PVC is easy to age and stain.
4. ABS edge banding can be directly burned at high temperature without air pollution; PVC produces toxic and irritating gases such as HF, HCL, SO2 and dioxin. This is the best way to distinguish between the two.
5. Since ABS edge banding is degraded by environmental protection, its flexibility must be sacrificed, so ABS edge banding is easier to break.
3. How to band the edge?
1. Manual edge banding
The machine used is relatively simple, the hot melt glue is heated and the edge is directly sealed, and then the edge is trimmed with a router or a utility knife. That’s it.
2. Heavy automatic edge banding machine
It can complete multiple processes such as board feeding, edge gluing, end cutting, trimming, corner rounding, scrapping and polishing at one time, realizing automatic edge banding.
3. Seamless laser edge banding
The laser polymer functional layer of the edge banding tape is instantly activated by the laser device, so that the edge banding tape and the sheet particles are “rivets” joined together.
The bonding strength between the special function layer and the edge banding tape is very high, just like a polymer as a whole, so the laser edge banding can be understood as only one “joining surface”, which greatly improves the bonding peel strength and enhances waterproof functions.
Features:
(1) Appearance effect: seamless effect, more beautiful, especially for light-colored panels such as white and transparent panels such as acrylic;
(2) Product quality: stable quality and high qualified rate;
(3) Processing cost: Gluing, spraying anti-sticking agent, workpiece heating, gluing, and squeegee units are omitted during edge banding processing, and the pressure roller and trimming knife are no longer glued, which reduces the use and labor costs;
(4) Energy-saving and environmental protection: There is no volatilization pollution of glue, no cleaning is required, the energy consumption of the machine is extremely low when idling, energy saving and environmental protection.
The following is a comparison of edge banding:
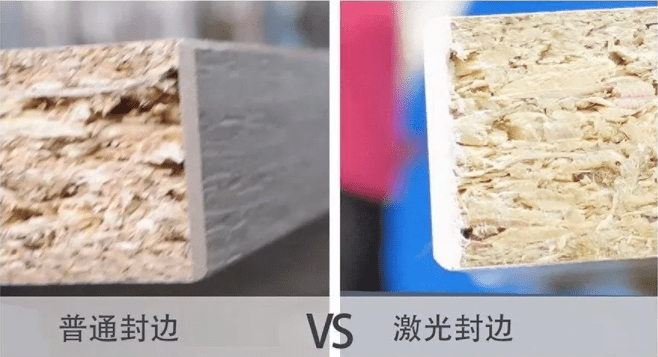
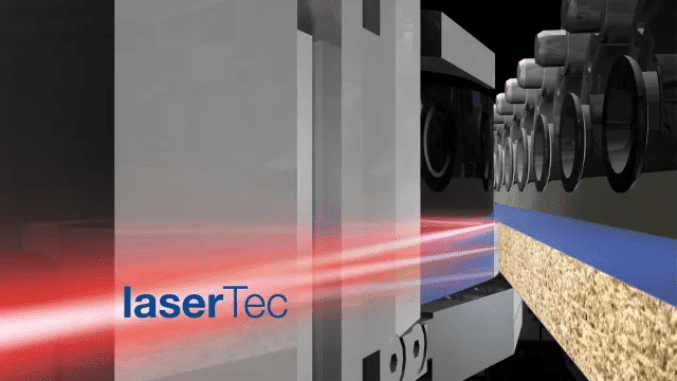
4. What kind of hot melt adhesive for edge banding?
The main components of hot melt adhesives are basic resins, tackifiers, plasticizers, and some other additives, among which the largest proportion is the basic resin, which is also the basis for the naming of hot melt adhesives. There are many kinds of hot melt adhesives, and appropriate adjustments will be made according to the specific materials that need to be bonded. However, according to the type of basic resin, it can be roughly divided into EVA hot melt adhesive, TPU hot melt adhesive, PES hot melt adhesive, and PA Hot melt adhesive, PO hot melt adhesive.
1. EVA hot melt adhesive
EVA hot melt adhesive is one of the most used hot melt adhesive products at present. This is because EVA itself has relatively strong material adaptability, and there are many types of materials that can be bonded.
2. PUR glue
(1) Compared with traditional hot melt adhesives, the bonding strength of PUR glue can be increased several times, especially the peel strength is significantly improved. This feature is suitable for special edge banding materials that require high bonding strength, such as aluminum and acrylic.
(2) Most hot melt adhesives are operated by heating, which can be reheated after bonding, which is reversible. The PUR edge-sealing hot-melt adhesive is a moisture-reactive hot-melt adhesive. After heating operation, it will react with the moisture in the air after being attached, and it will be irreversible after the reaction.